Filter Housing Assembly
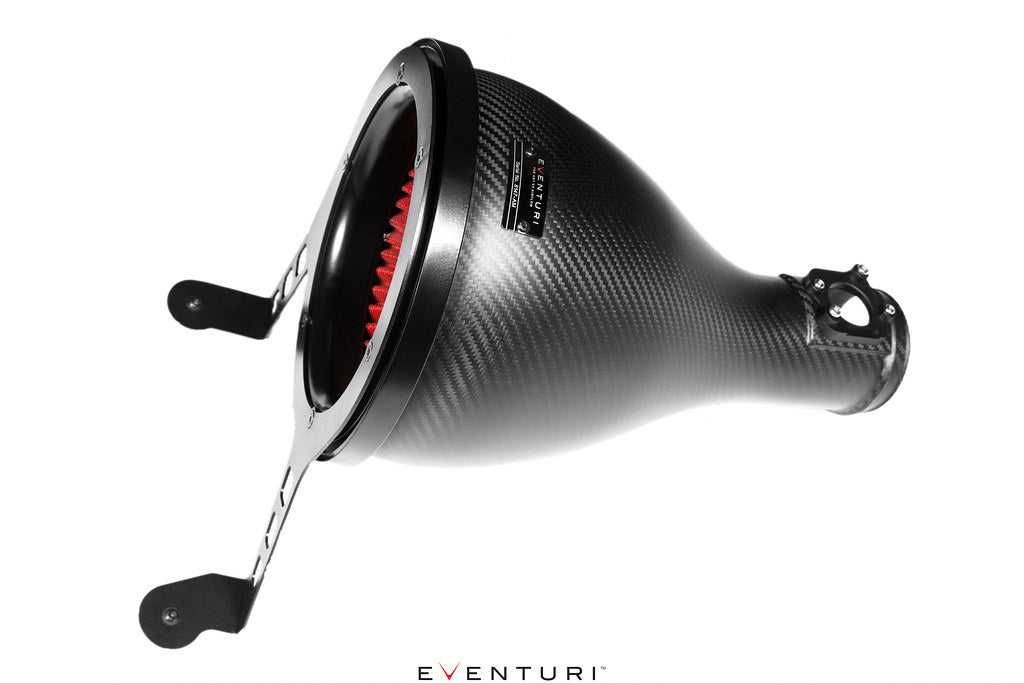
The filter housing comprises of our bespoke generation 2 filter, aluminium inlet cowl, stainless steel bracket and the integrated MAF section. The carbon pod shrouds the reverse mounted filter and smoothly shapes the airflow down to the MAF section which then connects to the rear inlet tube. This changes the flow path from the OEM airbox where airflow enters the front of the airbox, changes direction by 90 degrees to travel through the panel filter and then changes direction again by 90 degrees to move through the MAF section. Our system is a lot more direct with airflow entering the front of the filter housing and and moving into the MAF section without any abrupt direction changes. The result is a smoother path from the filter to the turbo inlet tube and therefore the turbo is able to function with less drag.
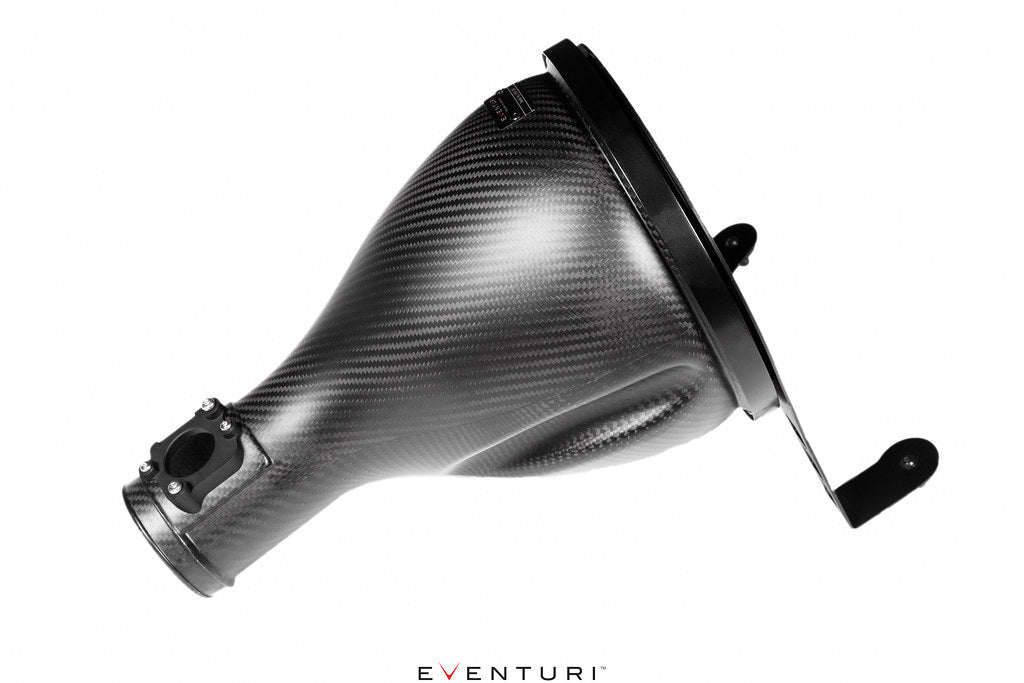
Bespoke Cone Filter
In order to achieve the highest flow rate possible we used our largest filter which has an outside diameter of 210mm or 8.3" and when flow tested with a housing using a 4" opening is able to flow up to 940 CFM at 28" H2O. The filter medium is ISO tested to ensure that filtration is in line with OEM standards and is also dry. The filter is constructed with our signature flow cones to aid in the Venturi housing principle.
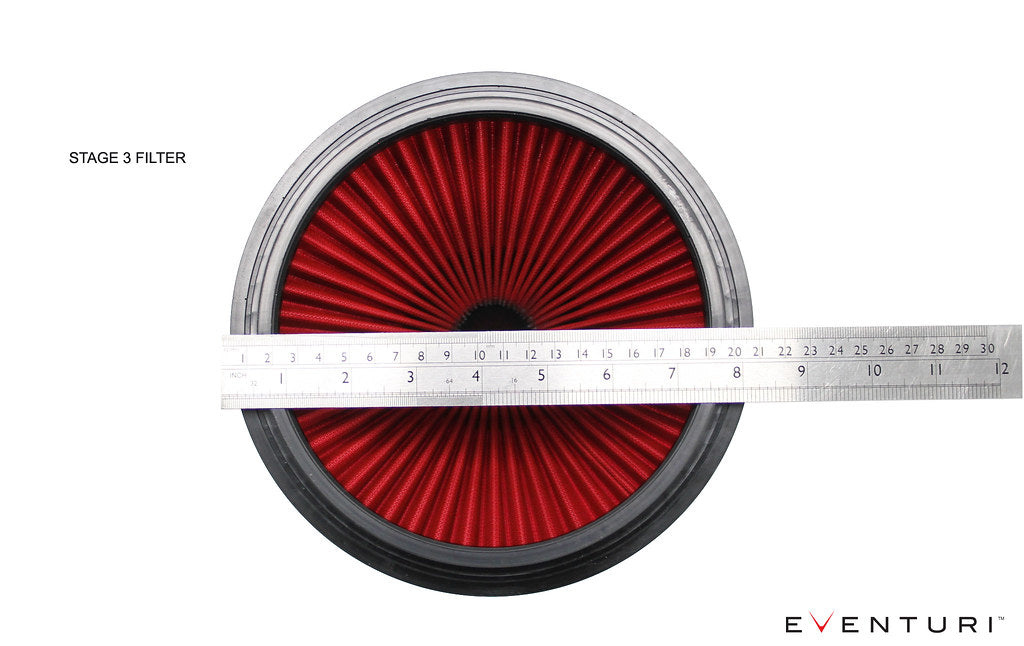
Patented Technology
Our patented filter housing has a smooth reduction in cross sectional area as it shrouds the filter and tapers down to the tubing. This geometry invokes the Venturi effect where the airflow accelerates whilst maintaining laminar conditions. It can be thought of as a large velocity stack - below is a diagram to show the comparison between our patented design and a regular intake system. Our bespoke filters aid the airflow moving through the housings and allow for an even velocity profile as the airflow exits the housings. Further details can be read in the Technology and Filters pages.

Carbon Duct
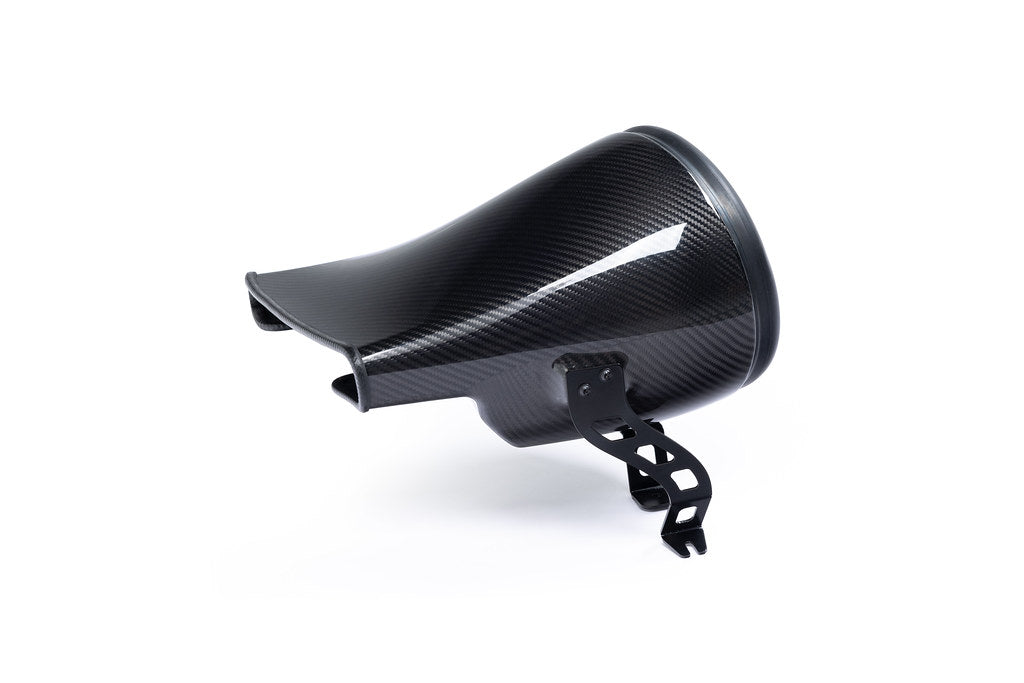
The duct feeds the filter housing with ambient airflow from the front bumper/grill section. We maintained as large a volume as possible all the way to the front of the engine bay and derestricted the front of the duct by creating an opening just behind the bumper where the bonnet would close. This area of the engine bay stays at ambient temperatures while the car is in motion through the help of our additional scoop and so the intake is able to draw in air without being restricted to the small opening on the slam panel. We did not extend the duct to the other side of the engine bay to use the second opening in the grill simply because of the abrupt flow angle and the restriction in space between the engine and the bonnet catch. Furthermore, using the second opening would stop cold air from entering the engine bay to assist with reducing overall heat soak. Finally the duct seals against the filter housing with an expanding rubber seal which allows for movement of the filter housing with the engine without letting hot air in.
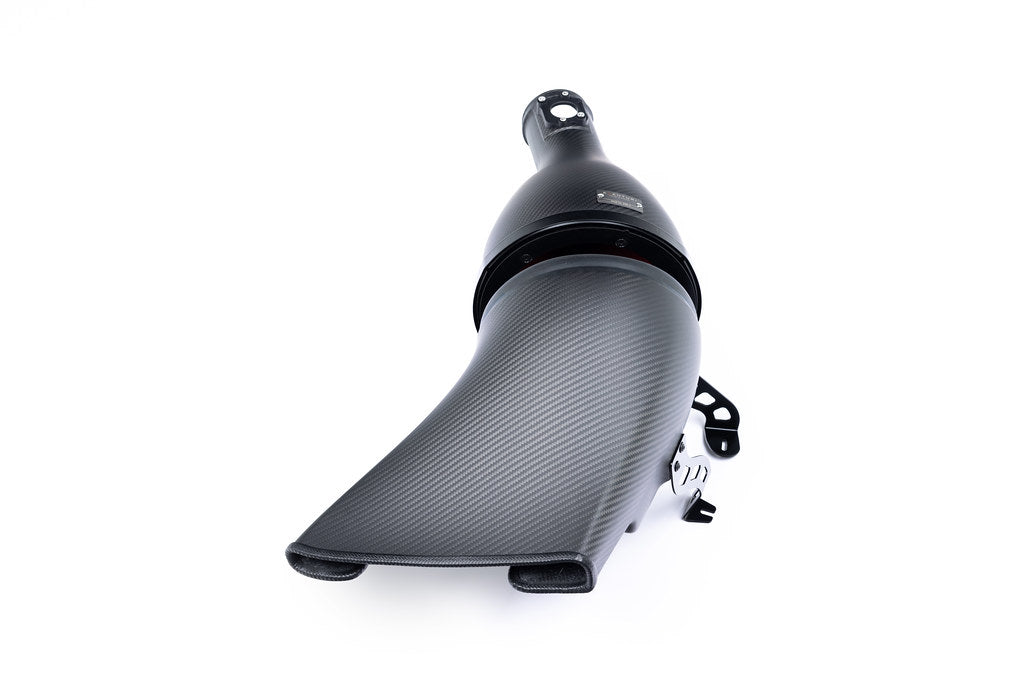
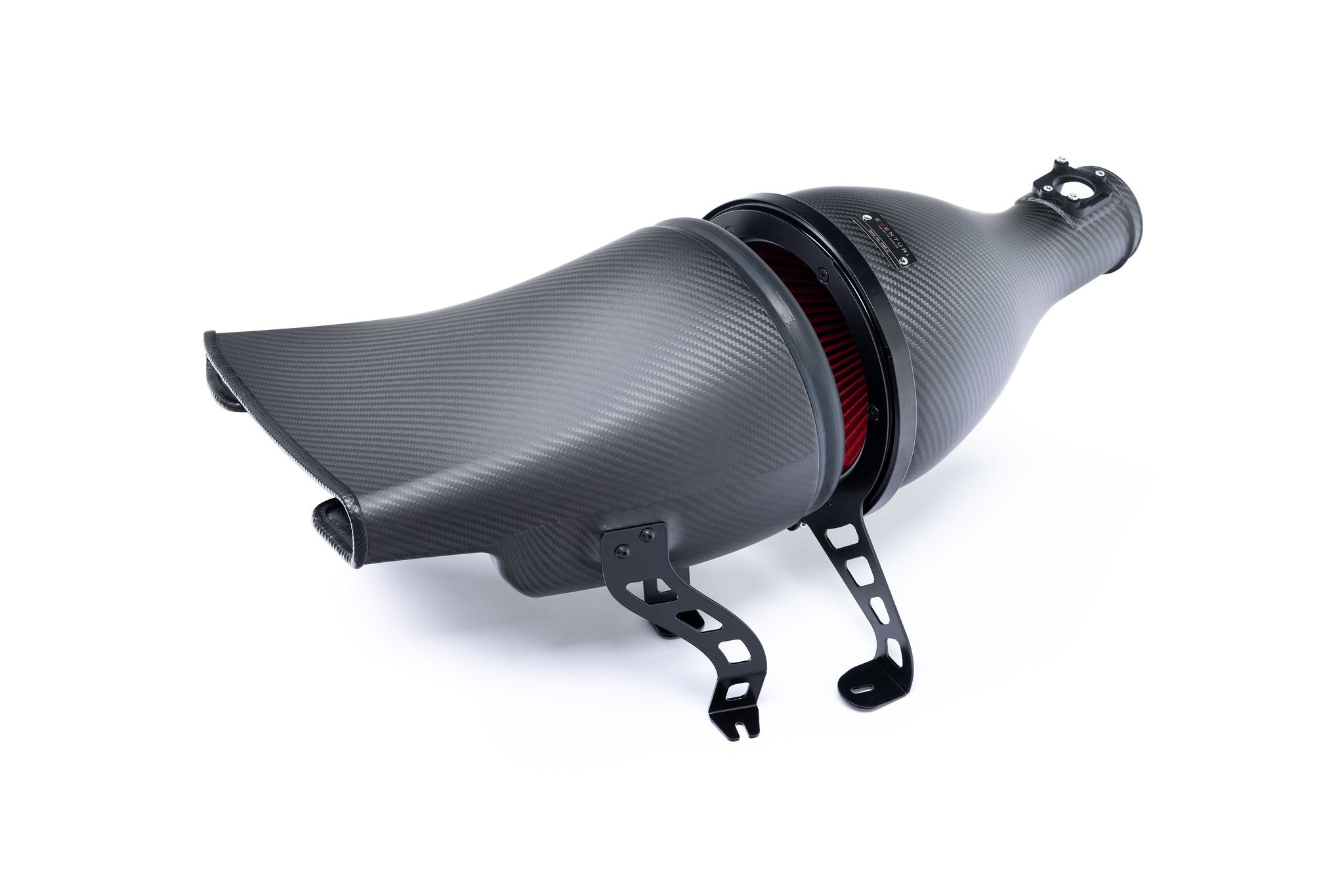
Rear Tube and EPDM Coupler
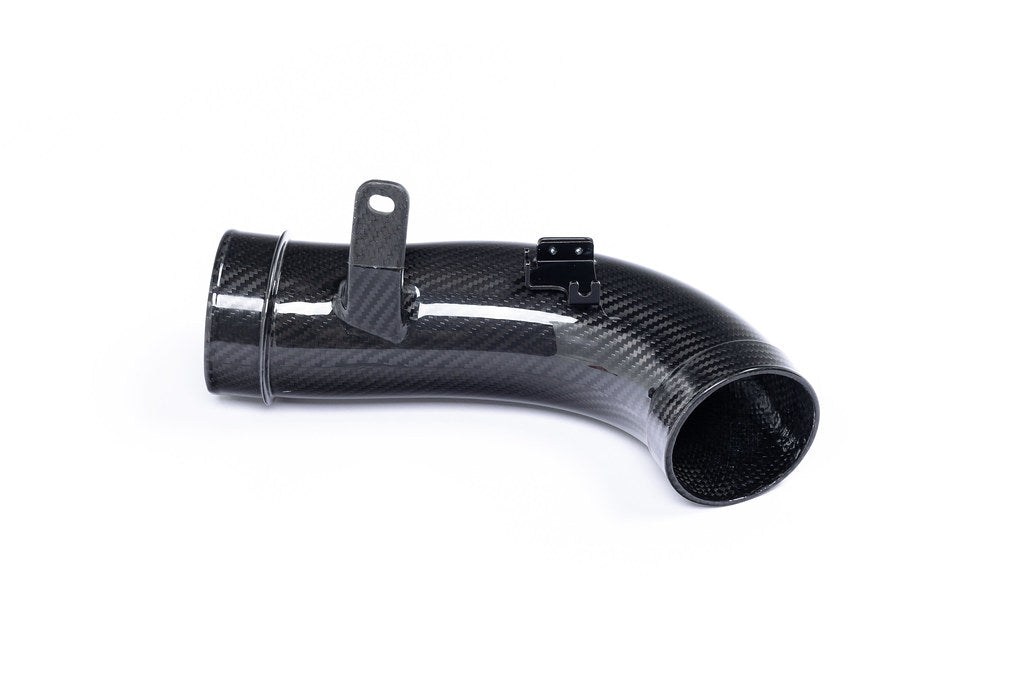
The rear tube has been developed through extensive CFD modelling to remove turbulence and maintain as smooth a path as possible. The OEM rear tube has a sharp internal bend radius and at high flow rates, this can cause unwanted turbulence which can affect the efficiency of the turbo. Several designs were tested in order to arrive at the most optimum shape which we then made from a high temperature carbon fiber. We redesigned the rear tube to allow for a smoother bend which also allowed for a more optimum positioning of the filter housing. The connection between this tube and the filter housing is achieved with a custom made EPDM coupler which allows for vibrations and movement of the engine.
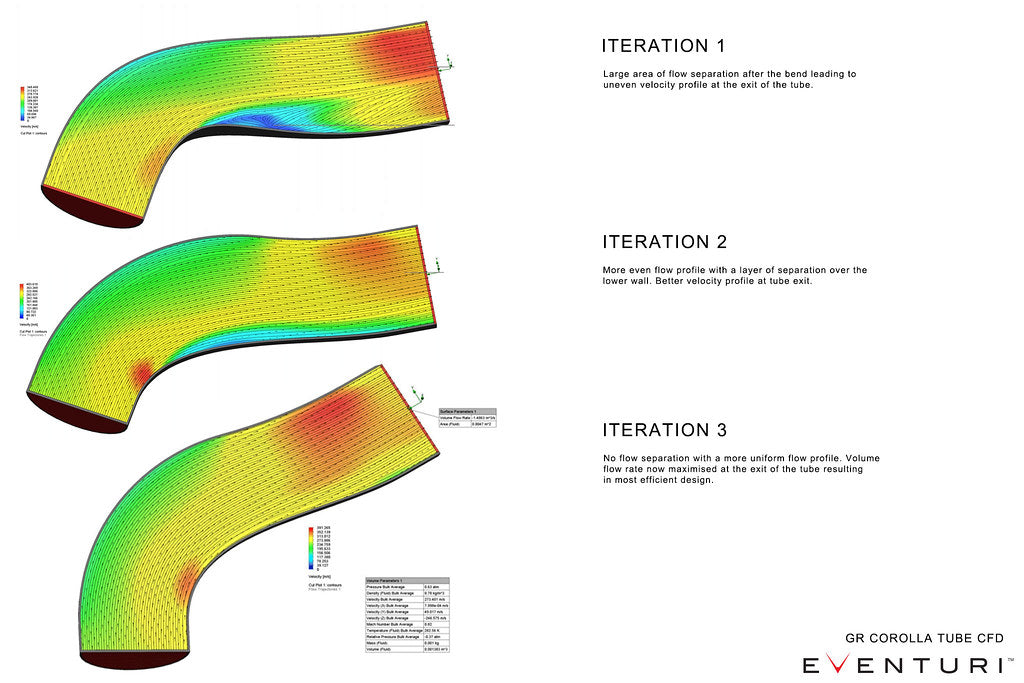
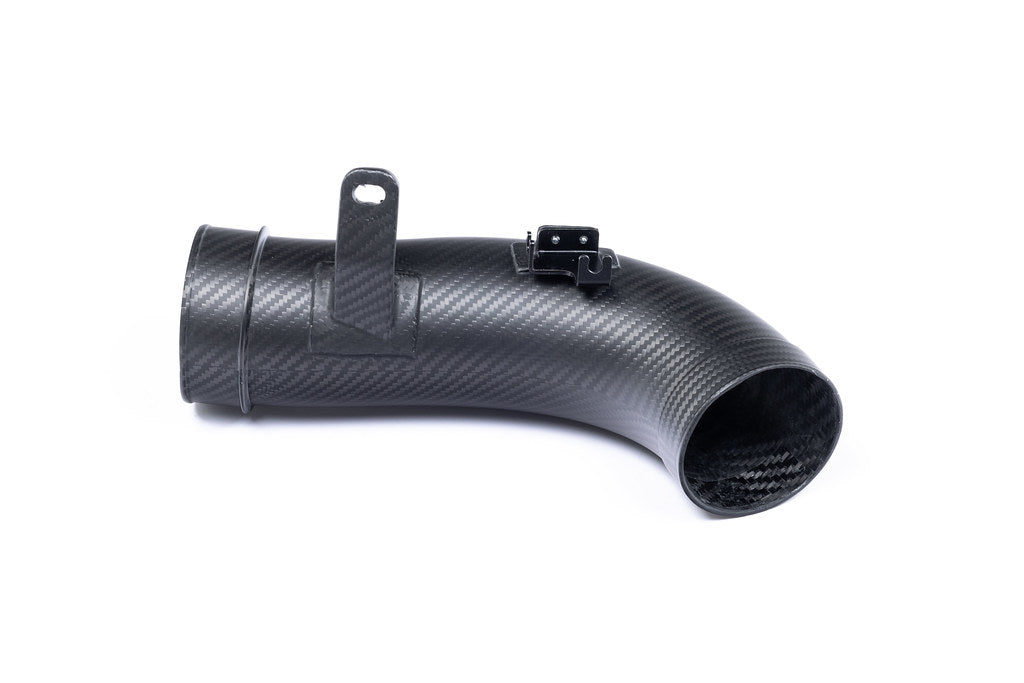
Front Scoop
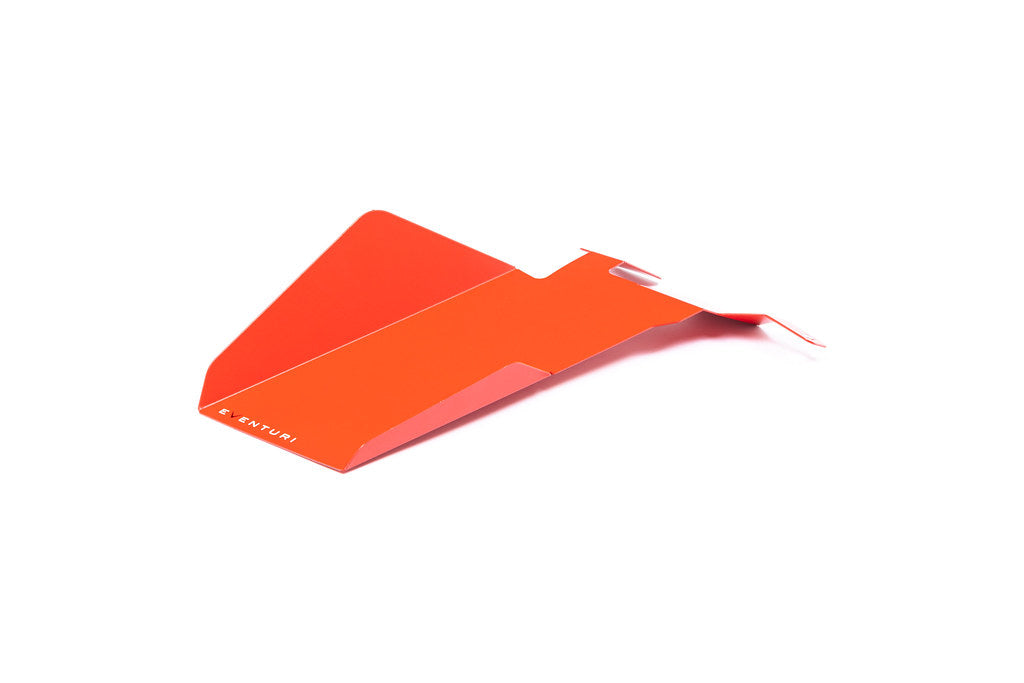
The final component is a front scoop which sits behind the grill to direct ambient air upwards into the opening of the slam panel. This aids in keeping IATs low while the car is in motion.